Contents
The duty cycle of a compressor dictates its longevity. The duty cycle of a compressor is the percentage of time that it can run before shutting off to cool down. If an application requires more than half-duty, then you need to know how much horsepower (HP), torque, and energy your air tools require. This will tell you how much air volume (CFM) and pressure (PSI) your compressor needs to produce.
How to Calculate Duty Cycle
How to Calculate Duty Cycle
You can calculate the duty cycle by dividing the running time by the total time. For example, if a compressor runs for 3 hours and has a whole time of 8 hours, the duty cycle is 37.5%.
Brief Examples
25% Duty Cycle:
When an air compressor’s duty cycle operates at 25%, it indicates that it will work for one-fourth of the one complete round time. If the compressor has a one-hour cycle length, then the run duration will be 15 minutes. As a result, every 45 minutes of operation would need 45 minutes of downtime. This type of compressor is ideal for small applications that only require intermittent power, such as portable compressors used in DIY tasks at home.
50% Duty Cycle:
A 50% duty cycle dictates that the compressor will run for half of the complete compressor round time. If the compressor has a one-hour cycle length, then the run duration will be 30 minutes. This type of compressor is ideal for basic household tasks such as inflation and trim work.
75% Duty Cycle:
A 75% duty cycle rating indicates that it will operate continuously throughout its three-quarter (75%) of an hour cycle length. If the compressor has a one-hour cycle length, then it will run nonstop for 45 minutes before needing 45 minutes of downtime to cool down. This type of compressor is a perfect option for medium-duty approaches like spray painting, stapling, and nailing.
100% Duty Cycle:
A 100% duty cycle rating means that this will run continuously for the entire length of the one-hour cycle. This type of compressor is ideal for high-demand applications like sanding or grinding. When using a compressor with a 100% duty cycle rating, be sure to allow for adequate cooling time in between uses to avoid damage.
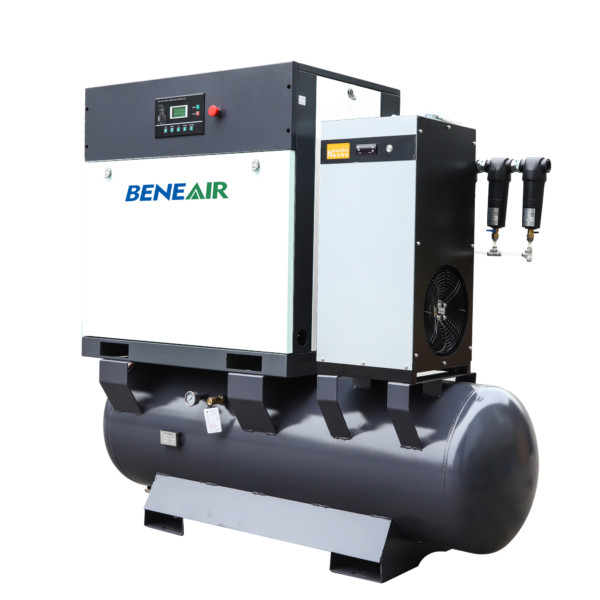
How to Extend the Duty Cycle of a Compressor
How to Extend the Duty Cycle of a Compressor
If you need to run your compressor for longer than its rated duty cycle, there are a few ways that you can extend its runtime.
- Use a larger air compressor. This will allow you to run more tools simultaneously and reduce the amount of time that each instrument is running.
- Use a pressure regulator on each tool. This will lower the air pressure going into the device and will decrease the amount of air that the compressor needs to produce.
- Install an after-cooler on your compressor. This will cool the air down before it enters the tank, which will help it last longer.
- Use a lubricated or greasy rotary screw air compressor. Rotary screw compressors reduce the amount of heat build-up because they are continuously cooled with oil instead of ambient air like reciprocating compressors.
- Install a belt guard on your electric motor to protect it from damage or burnout caused by dust and debris contaminating the belts and bearings inside the compressor tank.
Relationship Between Duty Cycle of Air Compressor with CFM
Relationship Between Duty Cycle of Air Compressor with CFM
The duty cycle regulates the run time of a compressor. The CFM required from the compressor to power a tool or application will determine what type and size of air compressor you need.
If your application requires more than half-duty, then you need to know how much horsepower, torque, and energy your tools require. This will tell you how much CFM and pressure your compressor must produce for your specific needs.
Increase in Air Compressor Duty Cycle
Increase in Air Compressor Duty Cycle
Without any means of cooling, rotary screw compressors are only 25% efficient at 100% duty cycle and 12.5% efficient at continuous operation because it has rotating parts that wear down over time. These types of air compressors typically have an after-cooler for this reason (to cool the discharged air).
As a general rule, most electric motor-driven air compressors are approximately 87%-93% efficient at 100% duty cycle, which is why they are widely used in construction sites where traditional air compressors would be too loud/hot/dangerous to work around continuously. However, a continuous operation, these types of air compressors typically cannot exceed 75%-80%.
Duty Cycle of Compressor with Different Types of Motors
Duty Cycle of Compressor with Different Types of Motors
The duty cycle on continuous running air compressors may be excellent, but the compressor motor itself can only operate at its peak performance for 30 minutes continuously. After that period, the compressor will need to stop and cool down before it can run again.
If you use an electric motor-driven compressor without a belt guard or pressure switch over 30 minutes continuously, the electric motor could burn out from overheating. This is because most electric motors are cooled by air passing through their casing and across their windings/brushes. If these parts become clogged with dirt and dust, they cannot dissipate heat properly, which causes them to overheat and burn out.
To prevent this, it is essential to use a belt guard on your electric motor and to install a pressure switch that will stop the compressor from running if it detects excessive heat/pressure.
In general, reciprocating air compressors have a less lengthy duty cycle than rotary screw air compressors. This is because they are continuously cooled with lubrication oil rather than air like other types of compressors (scroll, reciprocating). Continuous-duty rotary screw compressors may operate up to 24 hours/day without stopping.
Tips keep in mind while choosing a duty cycle for the compressor
Tips keep in mind while choosing a duty cycle for the compressor
- Selecting the correct compressor is key to meeting your CFM needs
- An air compressor’s duty cycle is determined by how long it can run at a consistent load without stopping
- The duty cycle will be affected by ambient temperature, load on the compressor, and type of motor
- A rotary screw compressor has a longer duty cycle than a reciprocating compressor
- It is important to use a belt guard and install a pressure switch to protect electric motors from overheating if running continuously for more than 30 minutes.
Though the duty cycle is a critical aspect of choosing a compressor, it should not be your only consideration when buying one. Duty cycle means how long your compressor can run without stopping and at what pressure/CFM to expect during that period. However, you must take into account other factors such as the type of air compressor motor and cooling system before making a purchase. This blog article is only to provide you with the basics of the duty cycle and how it affects your air compressor purchase.
Leave A Comment