Air Compressor for Textile Industry
Compressed air is an essential requirement of the textile industry nowadays. It allows low-cost operations in terms of energy consumption.
The air compressors are the pneumatic device. It converts chemical and electrical energy into potential energy in compressed air. An advancing textile industry works based on energy efficiency.
Therefore, it promotes cost-reducing techniques of using oil-free air compressors. There are multiple Applications of Air compressors in the textile industry to match modern needs.
Therefore choosing the best is the ultimate way to produce and process human-made or natural textile products.
Do you need
Do you need
for fewer rejections and better quality?
We have more than 30 years’ experience.
Application of Air Compressor In Textile
Air compressors have numerous applications in the textile industry. The fine yarn and vibrant color of the fabric are impossible without the air compressors in the industry.
- Air-jet weaving
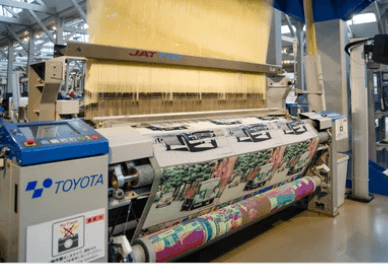
An air jet loom is a kind of weaving loom. The only difference is a loom without a shuttle. Instead, the air jets throw the weft yarn in the shed by the air compressors, consisting of the main nozzle, profile reed, and auxiliary nozzle.
Air-jet weaving transforms household fabrics like apparel of all kinds as well as industrial materials. Also possible are weaving plaids or jacquard fabrics. Air-jet looms have several advantages over shuttle weaving as they can process heavier yarns at a faster rate.
2 Spinning
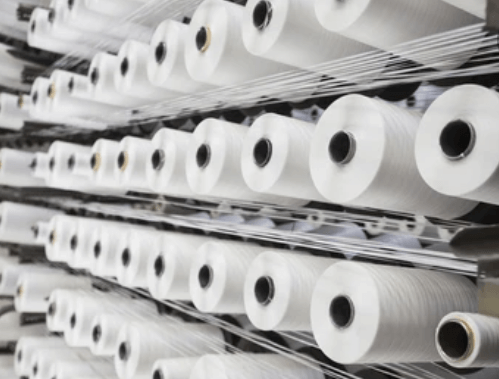
The spinning of yarn and thread is an essential yet critical task. Hence air-jet spinning avoids the damages.
3 Texturizing
An air compressor generates a fast air jet through a nozzle to intermingle the yarn.
4 Pneumatic transport
Compressed air generated from air compressors also eases the pneumatic conveyor of fabrics and PET chips.
5 Artificial fiber production
The partially oriented yarn (POY) production and fully oriented yarn (FOY) need air compressors to produce compressed air.
6 Coning, winding, and dyeing non-woven textiles
Transporting the spinning yarn to a reel or cone is done with compressed air in textile industries.
7 Wastewater treatment
The yarn and thread production uses a lot of water with hazardous chemicals. The dying and other strengthening processes need chemicals to treat fabric and yarn to produce a quality fabric. Unfortunately, such wastewater is harmful to natural systems; therefore, air compressors are an essential part of wastewater treatment plants.
If you are associated with any of the above industries, you would likely need air compressors for your products. The problem you could face while buying is the quality and price of the air compressor. To solve your problem BENEAIR has a wide range of air compressors with good build quality and a reasonable price.
The Advantages of Air compressor in the textile industry
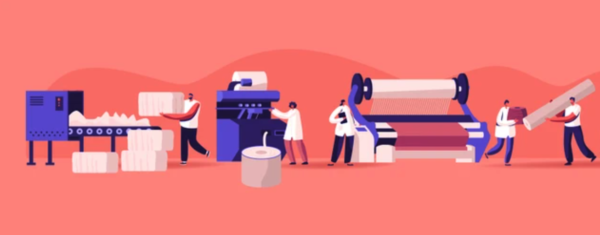
The correct types of equipment are vitally essential to meet the demands of the modern textile industry. In contrast, outdated devices and machinery will waste resources and produce quality compromised fabric and products. Therefore, using the latest techniques is an excellent opportunity to turn the challenge into a profit-generating moment.
High-Quality air compressors in the textile industry contribute to numerous competitive advantages. Here are some obvious benefits that you can attain using air compressors in the textile industry.
- Cost-effective operations
Compressed air assists textile manufacturers in overcoming various obstacles correlated with yarn and fabric production. The most significant factor among these benefits is cost-efficiency.
Good quality air compressors in the manufacturing unit ensure fast and efficient stock, adding competitive worth to the corporation itself.
- Increased productivity
Compressed air via air compressors also assists in supporting its tools and other maintenance equipment. It enables manufacturers to boost productivity rate and less time to mark the tremendous efficiency.
- Well managed waste production
Waste management utilizes the non-refundable resources of the industry. Therefore adding machinery that works using compressed air is a sustainable solution.
The Air compressors in the textile industry aim to decrease or productively regulate waste products.
Factors affecting Efficiency of Air compressor in textile industry
The Applications of Air Compressor in the textile industry is not replaceable with any other technique so far. Hence to enhance the efficiency and benefits of using the air compressors few factors play a vital role.
- Contaminated Air
A speck of dirt build-up inside the compressor can produce the contaminated compressed air. Therefore it requires regular cleaning and maintenance to work on the best form.
On the other hand, unattended machinery reduces the life span and efficiency with time.
- Humidity
Naturally, air contains water vapors. However, compressing becomes quite tricky and more energy-consuming because the air has a high level of humidity. Also, it can cause rusting of the metal parts of the compressor.
- Hot Air
Fortunately, cold air is convenient to compress. The colder air is already sufficiently compressed compared to hot air. Hence, it saves more time and resources to use cold air instead of hot air in air compressors.
Over the Horizon Applications of Air Compressor in textile industry
The textile industry has a high potential to absorb the latest techniques and replace traditional manufacturing systems. A minor cost-efficient shift regarding machinery affects the overall production cost to many folds.
Hence, the sophisticated and latest machinery helps the textile industry overcome the challenges. Simultaneously, it improves the quality of the textile products.
The future applications of Air Compressor in the textile industry have high potential as it tends to:
- Enhance the durability and potency to satisfy the desires of customers
- Reduction of production costs linked with operating and maintaining air compressor tools and systems
- Prevents flaws and contamination of air/fluid mixture in the production units
- Controls the excessive waste and perform a more sustainable operation in general
- Delays the aging and deteriorating production centers with modern equipment
The textile industry using compressed air is booming and flourishing like never before. Nevertheless, direct and indirect advantages run the textile industries at an optimum pace.
Common Equipment for the Textile Applications
- If the compressed air will be applied to textile industry, we suggest using 100% Oil-free type air compressor with the refrigeration air dryer and filters.
- For a low-risk compressed air for production line, if with a limited budget, the oil-lubricated type air compressor with refrigeration air dryer and filters can be chosen, but for long term consideration, an oil-free type air compressor can not only produce high-quality oil-free and clean air but also costs lower for maintenance and energy.
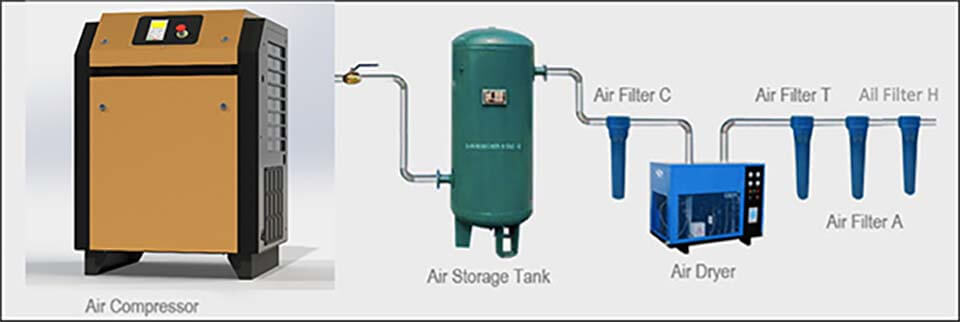
Related Products
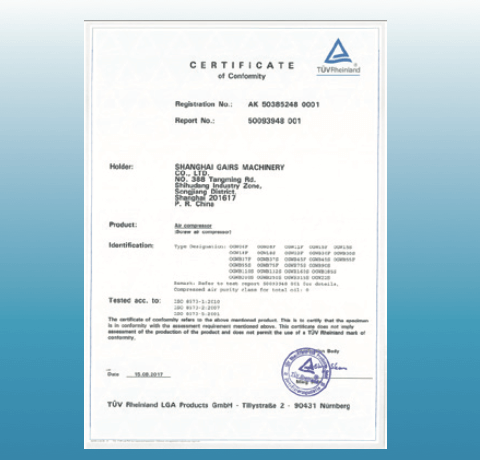
100% OIL-FREE
More than 20 years experiences in Water-lubricated Oil-free technology
Germany Rhineland TUV Class 0 Oil-free Certification
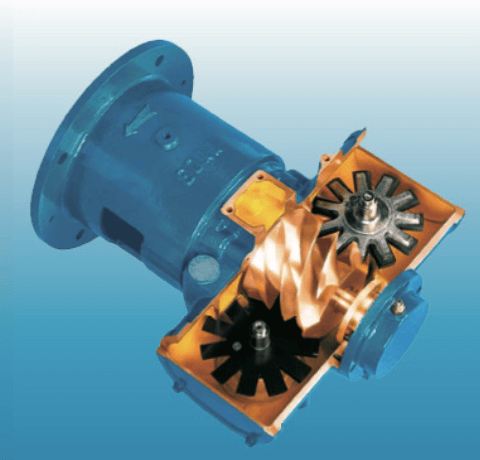
RELIABLE
More than 30 years Single Screw Technology
Most balance and reliable structure
Low temperature(< 55℃) reduces the stress on components
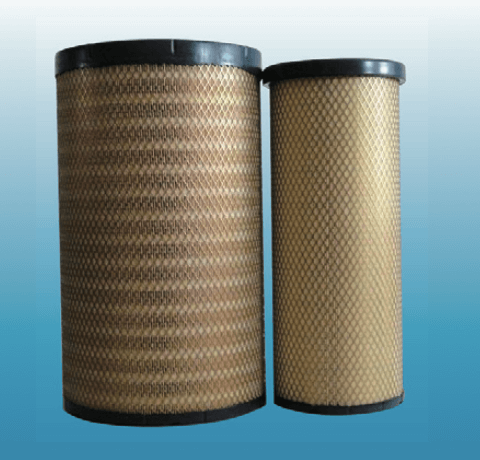
LOWER MAINTENANCE
Without Oil Air Separation Unit
Consumable parts are only air and water filter elements
$100~$300/year
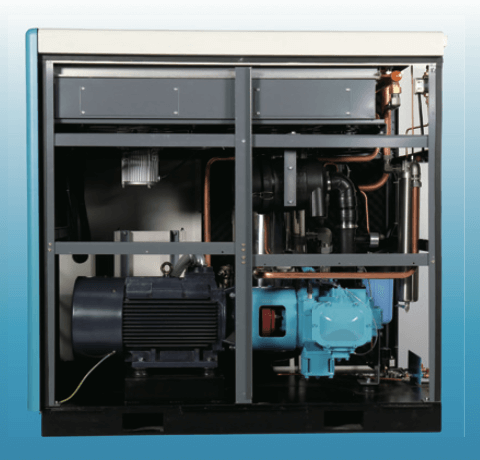
ENERGY SAVING>30%
Ideal isothermal compression and no heat waste(<55℃)
Most Advanced VSD and Two-stage compression technology
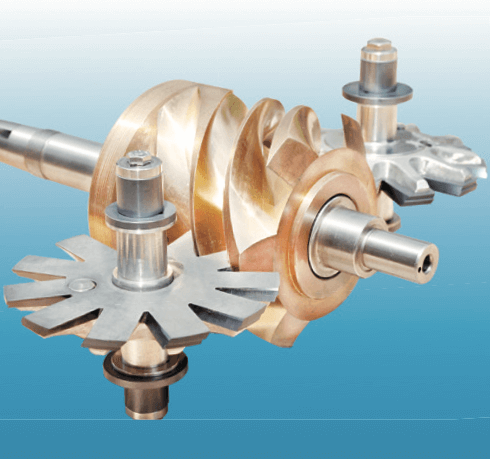
SUPER QUIET
Super dynamic balanced system
The motor and screw are directly connected
Sound absorbing materials are also used in the shell
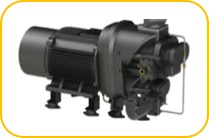
AIR END
Optimal profile
Double stage energy saving more than 10% than single stage.
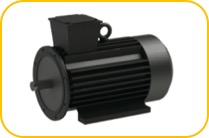
PM MOTOR
Direct Drive
Class 1 PM motor, Power factor: >95%, Oil-cooled type can be customized
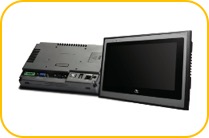
VSD CONTROL
Automatic operation
Dynamic display all operation parameters, prevent accidents by the alarm.
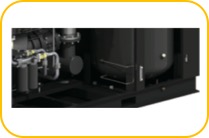
EASY-MAINTENANCE
Patent technologies
Filters can be easy replaced in half an hour. Oil can be completely replaced.
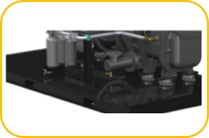
OIL SYSTEM
Minimum pressure drop
Patent oil storage device can guarantee the oil supply of the air end after a long shutdown.
How to choose the right air compressor?
Air Compressor for Dry Cleaning
Rotary screw compressors are commonly used in commercial settings such as dry cleaning establishments. The rotary screw compressor
The Future of Compressed Air Use
Rotary screw compressors are predicted to have a prominent role in the compressed air industry in the future.
Air Compressors in Electronics Manufacturing
Industrial air compressors are used in nearly every industry. Air is essential to many manufacturing processes, and compressed
Vacuum Pumps and Air Compressor: What’s The Difference
When it comes to industrial equipment, vacuum pumps and air compression systems are two of the most critical
A Guide to Dental and Medical Air Compressors
Air compressors are significant in various industries; it hasn't forsaken medicine and dentistry to illuminate with its sparkle.
Air Compressors for Mining
In ancient times, mining was genuinely a hectic task to perform. Workers get on their wits end after
We replaced 21 piston type compressors with one 40bar 10cubic Screw type compressor.
No more noise, no more spare parts and high maintenance fee.
We began to use their oil free type products since 1998, the products are very reliable.
Their Water-lubricated Screw Air Compressor can ensure the 100% oil free and clean compressed air for our processing, and ensure the high quality of our products.
The oil free type screw air compressor energy saving 38.6% compared with our used air compressor, and saving 25.8% compared with the new oil lubricated type screw air compressors.
“Class 0 oil-free air compressor guarantee the best quality of our end products”
“Electrical costs and maintenance fee is significantly reduced.”