Contents
An air compressor pressure drop is the lowering of air pressure during the compression cycle. This pressure loss is caused by the resistance of the air to flow through the compressor and can be reduced by increasing the compressor’s inlet size.
Causes of Air Compressor Pressure Drop
Causes of Air Compressor Pressure Drop
The leading causes of air compressor pressure drop are as follows:
Resistance to flow in the compressor:
The air compressor consists of rotating, meshing gears that compress the air. As the air flows through these gears, it experiences resistance, which leads to a pressure drop. The inlet port of the compressor can be made bigger to reduce this resistance.
Boundary layer separation:
As the air flows through the compressor due to the rotation of the gears, it experiences a thin layer of low-velocity air in which viscous forces are dominant. The boundary layer is defined as this layer of low velocity. The separation of the boundary layer from the main flow causes pressure loss in rotating compressors, but not stationary ones.
Restriction of the airflow caused by piping from the compressor to the point of use:
This usually requires a larger inlet size and can sometimes lead to a pressure drop across other components at higher pressures. The only way to reduce this pressure loss is by using different piping materials or increasing their diameter.
Incorrectly sized filters:
If there is not enough filter area provided for the application, it will cause significant resistance and cause a high-pressure drop. Remember that air filters are customarily sized based on a maximum allowable pressure drop rather than a minimum filtration rating.
Turbulence in the airstream:
The interaction of the air molecules causes this as they flow through the compressor and can be reduced by using smoother inlet shapes.
Unstable gas conditions:
If the gas being compressed is unstable, it can cause fluctuations in pressure that lead to a high-pressure drop.
Thermal expansion of the air:
The change in air temperature causes this as it flows through the compressor and can be reduced by using an aftercooler or more excellent.
Friction between the air and the compressor internals:
This is caused by the interaction between the air and the compressor’s internal components. A smooth interior surface finish will reduce this pressure loss to some degree.
Leaks in the compressor system:
Any leaks in the compressor system will cause a pressure loss and should be fixed as soon as possible.
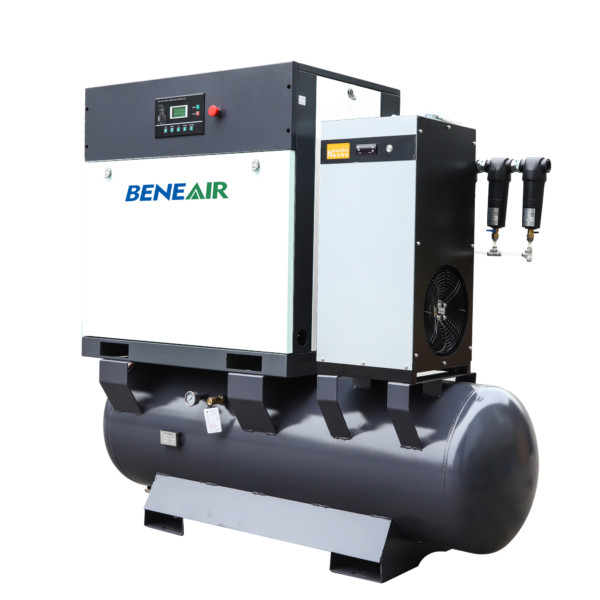
How Can Pressure Drop in Air Compressors Be Reduced?
How Can Pressure Drop in Air Compressors Be Reduced?
In order to reduce compressor pressure drop, there are several things that can be done:
Increase the size of the compressor intake:
This is the most effective way to minimize pressure drop and is usually the only option available for large compressors.
Use a larger diameter pipe from the compressor to the point of use:
This will help reduce the airflow restriction and use a larger compressor intake.
Increase the size of the filters:
If the filters are too small, they will cause a high-pressure drop. The pressure drop can be reduced by increasing the size of the filters.
Use smoother inlet shapes:
This will help reduce turbulence in the air stream and can be used with other methods to reduce pressure drop.
Install an aftercooler or cooler:
This will help reduce the thermal expansion of air and can be used with other methods to reduce pressure drop.
Use a high-quality compressor internal surface finish:
This will help reduce the friction between the air and the compressor internals and can be used with other methods to reduce pressure drop.
Fix any leaks in the compressor system:
Leaks will cause a pressure loss and should be fixed soon as possible.
By understanding what causes air compressor pressure drop, you can take steps to minimize it and ensure that your compressor is running at its most efficient level.
Signs that show that there is a pressure drop in the compressor
Signs that show that there is a pressure drop in the compressor
- If the pressure drop is high, it can cause the compressor to cycle on and off more frequently or even trip the overload protection. This will result in less production and higher operating costs.
- A sign of pressure drop in your compressor system is if you hear the compressor cycling on and off more frequently than average or if it trips the overload protection. Troubleshooting and fixing the problem as soon as possible is crucial if you notice this happening. Otherwise, you could see a significant decrease in production and an increase in operating costs.
How to avoid pressure drop in a compressor
How to avoid pressure drop in a compressor
If you are worried about a pressure drop in your compressor, there are a few things that you can do to avoid it.
-
- Reevaluate how much air your facility needs. If the filters are too small or the pipes are smaller than they need to be, they will cause an increase in resistance and lead to a high-pressure drop.
- Check for leaks by listening for changes in noise levels from the compressor system.
- Use more powerful components like increased horsepower compressors and bigger intake pipes. This is one of the most effective ways for increasing production while also reducing power consumption and operating costs at the same time.
- Keep your compressors as big as possible. A smaller compressor than necessary will lead to a higher pressure drop because there is less space for the air to flow.
Several factors can cause air compressor pressure drop, but there are ways to minimize it and keep your compressor running at its most efficient level. By understanding what causes a pressure drop and using the appropriate methods to reduce it, you can ensure that your compressor runs as smoothly as possible.
Leave A Comment