Air Compressor for Cement Industry
Air compression is a vital component in multiple stages of the cement mixing and manufacturing industry.
Air compressors and pneumatic conveyors allow effective processing with reduced effort, time, energy consumption, and contamination of the cement output produced.
Do you need
Do you need
We have more than 30 years’ experience.
Applications of Air Compressor in Cement Industry
Silo Control and Transport
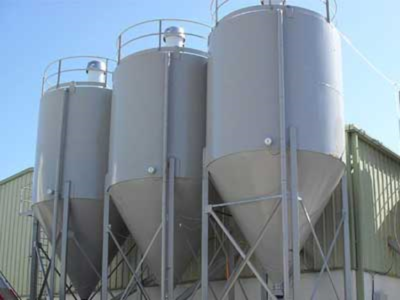
Storage silos are found in ready-mix concrete batching plants where tankers deposit fluidized powder through pneumatic conveying.
Air compressors in the tankers use air discharge controls to pressurize tanker vessels and fluidize powder in and around the distributor planes of the tanker.
The air compressor also has an essential role in distributing the fluidized powder from the tankers to pipes that run into the cement silos.
Air is ventilated through filters in the silo to avoid damage to machinery and if the air is improperly ventilated, the consequences could include over-pressurization in the silo.
Over-pressurization can be a safety hazard and can damage factory equipment through silo explosions, silo lid damage, and faults in the filtration systems.
Ash Handling Systems
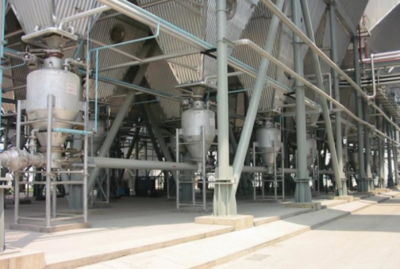
The combustion processes in cement manufacturing produce ash and thus require conveyance and loading of ash.
Fly ash handling systems are popular in the cement manufacturing industry and deliver fly ash from thermal power stations to storage silos used in cement making.
Cement factories employ transferal air force in their air compression mechanisms to handle and transport ash through smaller ash conveyor pipes.
Air compression helps cement factories save on space and energy consumption in the ash handling process.
Wet Process Clinker Plants
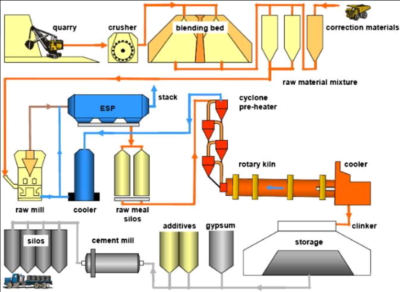
In a wet process clinker plant, calcareous materials are crushed and argillaceous materials are mixed with water.
The two materials are then combined together for the final stages in the cement manufacturing process.
Wet Process Clinker Plants use air compression to mix raw materials in cement manufacturing.
The mixture is turned into a “slurry” material and transported to the cement kiln for further processing.
The raw meal is pyro-processed and undergoes calcination and linearization to produce clinker, a substance that is cooled in the next step of the process.
A high amount of energy is trapped into this cooled air, also known as combustion air, and the cooled air travels into the cement kilns to process the clinker further.
De-dusting
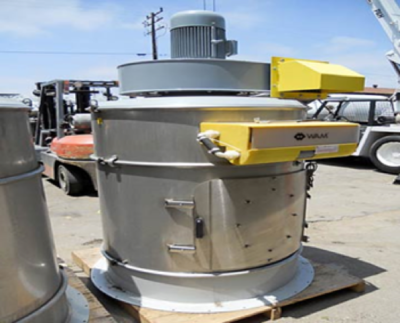
Air compression is used in de-dusting in the cement industry since a dust collection system in a cement plant uses air compression for dust removal.
A specific air weight in an air inlet pressure is distributed through pulse valves to bags in the system.
A pulse nozzle controls the weightage of compressed air, a crucial step as the dust collection systems need accurate levels of air pressure from the machine operators.
A specific rate of flow of compressed air required for the dust collection system’s efficient functioning and for effective repeats of the dust collection process.
Baghouse filters in a dust collection system need to be monitored on a regular basis to ensure decreased chances of corrosion and longer lifespans of the system as a whole.
Pneumatic Actuators
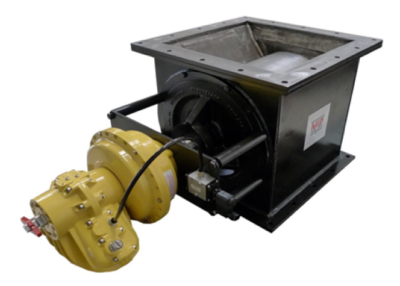
Pneumatic actuators are devices that create rotary or linear power forces through the use of air and pneumatic controls and actuators are used to power the rotary movement of valves in a cement factory.
Compressed air is an integral component of pneumatic actuators and pneumatic controls in the cement manufacturing industry.
Air compression must be optimal and contaminant-free because oil, dust, and water will corrode and deteriorate pneumatic system processes.
Common Equipment for the Cement Applications
- If the compressed air will be applied to the cement industry, we suggest using a Super energy saving Two-stage Oil-lubricated type air compressor with an air dryer and filters.
- If with a limited budget, the regular single-stage oil-lubricated type air compressor with refrigeration air dryer and filters can be chosen, but for long-term consideration, an oil-free type air compressor can not only produce high-quality oil-free and clean air but also costs lower for maintenance and energy.
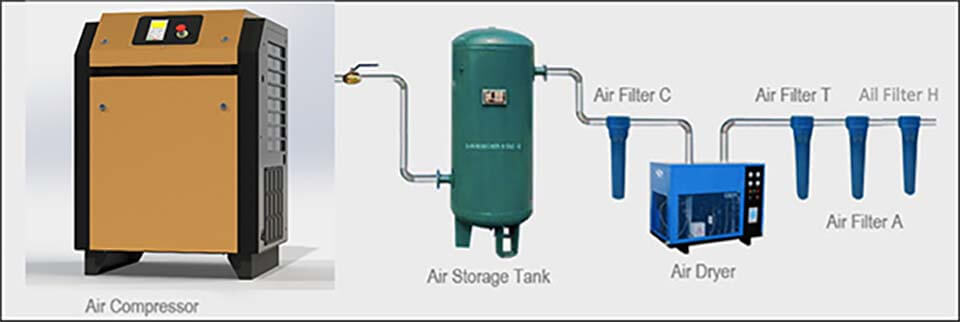
Related Products
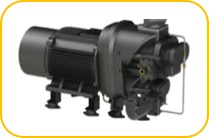
AIR END
Optimal profile
Double stage energy saving more than 10% than single stage.
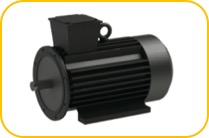
PM MOTOR
Direct Drive
Class 1 PM motor, Power factor: >95%, Oil-cooled type can be customized
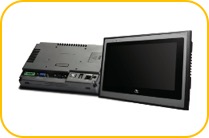
VSD CONTROL
Automatic operation
Dynamic display all operation parameters, prevent accidents by the alarm.
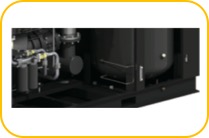
EASY-MAINTENANCE
Patent technologies
Filters can be easy replaced in half an hour. Oil can be completely replaced.
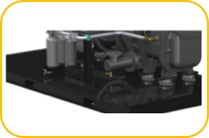
OIL SYSTEM
Minimum pressure drop
Patent oil storage device can guarantee the oil supply of the air end after a long shutdown.
How to choose the right air compressor?
Air Compressor for Dry Cleaning
Rotary screw compressors are commonly used in commercial settings such as dry cleaning establishments. The rotary screw compressor
The Future of Compressed Air Use
Rotary screw compressors are predicted to have a prominent role in the compressed air industry in the future.
Air Compressors in Electronics Manufacturing
Industrial air compressors are used in nearly every industry. Air is essential to many manufacturing processes, and compressed
Vacuum Pumps and Air Compressor: What’s The Difference
When it comes to industrial equipment, vacuum pumps and air compression systems are two of the most critical
A Guide to Dental and Medical Air Compressors
Air compressors are significant in various industries; it hasn't forsaken medicine and dentistry to illuminate with its sparkle.
Air Compressors for Mining
In ancient times, mining was genuinely a hectic task to perform. Workers get on their wits end after
We replaced 21 piston type compressors with one 40bar 10cubic Screw type compressor.
No more noise, no more spare parts and high maintenance fee.
We began to use their oil free type products since 1998, the products are very reliable.
Their Water-lubricated Screw Air Compressor can ensure the 100% oil free and clean compressed air for our processing, and ensure the high quality of our products.
The oil free type screw air compressor energy saving 38.6% compared with our used air compressor, and saving 25.8% compared with the new oil lubricated type screw air compressors.
“Class 0 oil-free air compressor guarantee the best quality of our end products”
“Electrical costs and maintenance fee is significantly reduced.”