Contents
Almost all air compressor setups have considerable and often unused energy-saving potential in the process of waste energy conversion. Energy expenditures can account for up to 80% of the entire cost of air compressor supply in major companies. But, by recycling the heat produced by air compressors, you might well be able to decrease your plant’s overall power usage.
You will save bucks and consume less power as a result. You can also have a reliable alternate heat source and reduce your carbon footprint. Latest rotary screw compressors are ideal for heat recovery because of their entirely enclosed construction.
How Much Heat is Being Produced Through an Air Compressor?
How Much Heat is Being Produced Through an Air Compressor?
Kilowatts and BTUs are two ways to measure the output of a machine. 2,545 BTU per hour is the equal of one horsepower. Although most air compressors are manufactured in conventional horsepower sizes, they may reach regulated compressor discharge levels and maximum capacity production by operating at workloads 10% higher than the generator labeled capacity.
The thermal energy ratio varies depending on the compressor type. The most popular compressor used in industrial facilities nowadays allows heat recovery easily. The lubrication cooler eliminates roughly 80% of the heat generated by these compressors. The aftercooler discharges the majority of the residual heat, with a tiny amount being evacuated as heat energy from the compressor chamber and lubrication divider collector. Most of the other discarded Energy is equally distributed between the aftercooler and intercooler together in a two-stage rotary screw compressor. Each discards 40% of the heat energy, while the chambers contribute 20%.
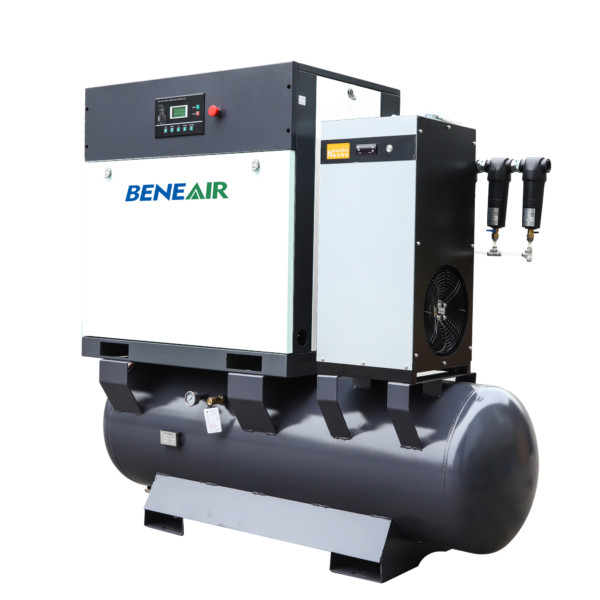
How does the Air System Heat Recovery from Air Compressors Work?
How does the Air System Heat Recovery from Air Compressors Work?
If the compressor has a fluctuating capacity, the amount of retrieved heat energy will evolve and change. A comparable, somewhat consistent heat energy supply is required for restoration to be possible. The ideal way to recover large amounts of heat is to enhance the energy provided to the unit. When the compressor is running, the amount of energy is always utilized.
Advantages of Air System Heat Recovery
- Lower Energy Expenses
Throughout the working period, energy expenditures can make up a significant portion to 80% of system costs. These expenditures can be considerably lowered by implementing heat exchange.
- Reduce Carbon Emissions
As power is used more economically, heat recovery reduces a company’s Carbon footprints.
Challenges for Air Heat Recovery System
- A limiting element is a range between the rotors and the facility that has to be heated up. This distance should be maintained as little as possible.
- Recovery may only be possible during the colder months of each year. Small or medium compressors are more likely to use air resource recovery.
- Excess heat restoration from compressor conventional cooling systems results in minimal energy losses and needs little financing.
How does the Air System Heat Recovery from Air Compressors Work?
How does the Air System Heat Recovery from Air Compressors Work?
- Heat Ventilation
The heat exchange ventilation process is an efficient heat energy reusing way to use in homes to prevent humidity from producing dampness that may create fungus and mold, which might ruin your residence.
- Common Usage
- Providing fuel for central heating systems.
- Amenities for doing laundry.
- Energizing.
- Processing Thermal Energy.
- In the food processing industry.
- Warm water is used to wash dishes.
- Warming a hot tub.
- Baths and restrooms supply hot water.
- Industrial Usage
Heated air supply from air compressors may be directed to evacuate or supply heat in the pump chamber and surrounding spaces using typical HVAC ducting and valves.
- Heaters for inventories or storage facilities.
- Heat for production systems and workplaces.
- Spraying airstream for drying out the paint.
- Air screens.
- Pre-heating compressed air to streamline the process.
- Water Heating
The heat that has been discarded can be repurposed to boil the water or other industrial fluids. This can be achieved with either air or water-cooled compressors, but for efficiency gains, water-cooled compressor facilities releasing chilled water directly attached to a continual process heat exchange assignment like a heating boiler are normally the most efficient.
- Plate heat exchanger usage is a profitable technique to recover heat from any air compressor and use it to boil or warm water for a variety of applications, including plating, chemical industries, and washing activities.
- Fail-safe heat exchangers give another form of security regarding compressor cooling medium pollution of treated water or liquids. As a result, they are more suited to thermal systems in the pharmaceutical and food industries, as well as for drinkable heating water.
Energy Efficiency Analysis
It is also vital to evaluate heat exchange to the present source of power for supplying thermal energy, which might be a low-cost energy source like hydrocarbons when estimating cost savings and reviving times for heat exchange facilities.
You can use the following calculation to figure out how much energy you can save by recovering heat:
Energy savings = (Compressor bhp) * (2,545 Btu/bhp-hour) * (Operating Hours) * (Revived heat energy percentage).
Cost Saving Analysis
You may also calculate how much heat you will be able to recapture. You can do this to determine how much you can save. You will have to have the values for Compressor horsepower, Compressor operating hours, Unit of fuel, and Expense of a component of energy to calculate your cost savings.
In general, the bigger the unit, the quicker the repayments, although the quantity of discarded heat that can be reused and the expense of the alternate fuel also play a role. You will need one additional calculation to calculate your cost savings:
Cost savings (per year) = (Btu/year of energy savings) / (Btu/unit of fuel) * (cost of unit of fuel)
Factors to Consider While Recovering Heat from Air Compressors
Factors to Consider While Recovering Heat from Air Compressors
Reaching out to a compressor professional is the very first phase towards retrieving energy from your compressor. Skilled experts will assess your compressor as well as your heating requirements. They can assist you in figuring out how to recapture energy from your compressor in the most efficient way possible.
Other techniques to get more energy-efficient output might include:
- repairing a leakage.
- Adjusting the psi of your equipment.
- Improvements that have been planned.
- Recycling heat usually necessitates the purchase of extra equipment or modifications. Heat exchange solutions are possible on certain contemporary compressors.
Leave A Comment