Pharmaceutical/Medical Air Compressor
Why Class 0 Oil-free clean and dry compressed air is required for the pharmaceutical industry or medical industry?
Such as tablets, pills, capsules, ointments, creams, gels, and syrups. The compressed air comes into contact during almost every step of the production process: mixing, granulation, drying, pressing, coating, and packaging. And the containers like bottles, tubes, and cans also should be cleaned and dried before filled with the drugs.
Do you need
Class 0 Oil-free compressed air systems for your Contact pharmaceutical processing line?
Do you need
for your pharmaceutical processing line?
We have more than 30 years’ experience.
Typical Applications for Pharmaceutical Compressor
The Common Applications for pharmaceutical Compressors? |
|
---|---|
Bottling/Packaging/Canning | For blister packaging machine, powered by PVC material blow molding
For capsules & tablets printers For medical bottle-making blowers For automatic cartooning machines For three-dimensional packaging of transparent film For automatic filling and sealing machines |
Cleaning | Manufacture plastic containers, blow bottles, and ampoules in a sterile area after cleaning with the compressed air.
Bottles, tubes, vials, and various types of packaging need to be cleaned and dried before use. These packages contact the product directly, so the air must be completely dry and free of oil. For example, used in ultrasonic bottle washing machines for 1-20 ml size ampoules, 2-100 ml syringes, molded bottles, oral solution bottles, etc., to provide power for the complete removal of impurities from the bottles. |
Smashing, grind and micronizing powders | For airflow grinders, traditional Chinese medicine crusher, rotary tablet press, capsule polishing machine, etc., to remove dust and impurities in time. |
Preparations | Filling machines for liquid preparations.
Used in capsule filling machines to discharge the filled capsules in time to prevent interruption of the filling process due to untimely discharge. Demanding applications such as encapsulation of needles, filling of powdered needles, etc., Spraying device for coating machines. Compressed air provides the power for spraying liquid or binder by the spray gun, and the power for removal of the dust. For one-step granulators (also called boiling granulators, fluidized spray granulators, fluidized bed granulators, etc.) It is used in high speed mixing and pelletizing machines to provide a sealed environment and a certain amount of power for this process so that the materials can be mixed evenly, and also to provide greater power for the discharge and feed of the material. |
Active Pharmaceutical Ingredients(APIS) | For slagging discharge of extraction and concentration tanks in the extraction process.
For Seedling fermenters, Semi-finished vaccine product preparation, Dilution tanks for mixing raw and prepared liquids. For herbal sterilization devices that provide an airtight environment for better sterilization. |
Instrumentation | For pneumatic conveying during the manufacturing process.
For the control valves, sorting, polishing, and more. |
Wastewater treatment | The used water during the manufacturing process needs to be treated in a cast that contaminates the product. |
Typical Applications for Medical Compressor
Some common applications include:
- Ventilators
- Hospital Oxygen Generator
- Respiratory equipment, oxygen concentrators, nebulizers
- Dental beds/seats/chairs, dental milling machine
- Surgical instruments
- Blood-analyzers
- Chiropractic & physiotherapy tables
- Endoscopy equipment
- ENT air/vacuum aspirators
- Evacuation/sealing/welding of bags/bottles (blood)
- Autoclaves
Quality Requirements for Pharmaceutical/Medical Compressor
In the Pharmaceutical industry, the compressed air should be purified of contaminants before use. General contaminants are solid particulates, water vapor, and moisture, oil vapors. Which are in the atmospheric air, the lubricating oil for oil-injected type air compressor, the pipes, storage air tank, and distribution.
When the compressed air has a direct connection with Pharmaceutical or medical products, we must ensure purity and cleanliness to prevent contamination. For the details what we should do are as follows:
Remove the moisture
As we know, moisture is good for microorganisms and fungus growth. If there is moisture inside the pipes of the compressed air, it is easy to be blown to the products or the packaging or containers. So we need to use dryers to ensure the required dew point. Generally, for the direct contact compressed air, the dew point should be -40℃ and use a desiccant air dryer, and for low-risk non-contact compressed air, the dew point can be 3℃ and use a refrigeration air dryer.
Remove the oil
The oil exists in the atmospheric air, so even you choose a 100% oil-free type air compressor, there is still oil vapor in the compressed air, so the filters should be used.
Generally, for direct contact compressed air, use an oil-free type air compressor is a must. Ensures Class 0 100% oil-free compressed air with high purity, eliminates the health risk of rejection risk associated with oil contamination. For low-risk non-contact compressed air, we can use an oil-lubricated type air compressor which is more economical, but it’s better to use filters to ensure the oil content 0.003ppm.
Remove the particles
The atmospheric air includes solid particulates or dust that may cause contamination if contact with the food products. Other contaminants may come from internal mechanisms of the air compressor system. We also need to use filters to ensure the particle content is no more than 0.01μm.
Common Equipment for the Pharmaceutical/Medical Applications
- For the direct contact compressed air for production line, we suggest using 100% Oil-free type air compressor with the desiccant air dryer and filters, the materials should be used is food-grade stainless steel.
- For the non-contact low-risk compressed air for production line, if with a limited budget, the oil-lubricated type air compressor with refrigeration air dryer and filters can be chosen, but for long term consideration, an oil-free type air compressor can not only produce high-quality oil-free and clean air but also costs lower for maintenance and energy.
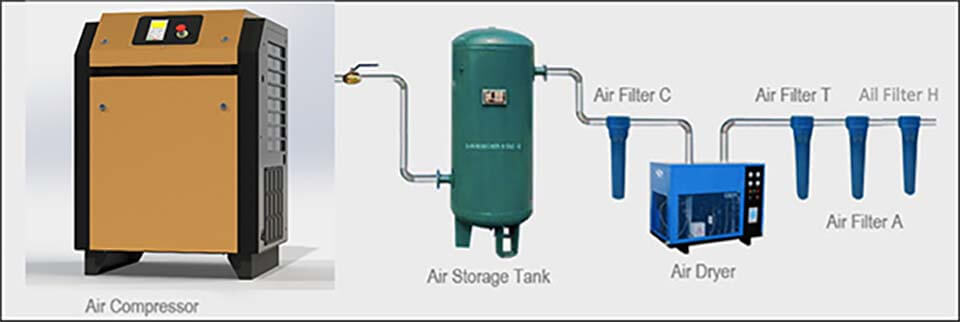
Related Products
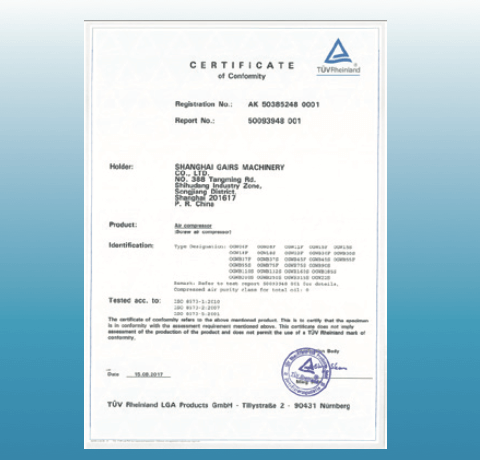
100% OIL-FREE
More than 20 years experiences in Water-lubricated Oil-free technology
Germany Rhineland TUV Class 0 Oil-free Certification
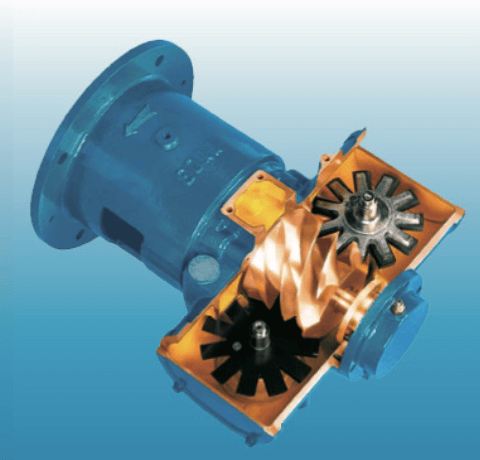
RELIABLE
More than 30 years Single Screw Technology
Most balance and reliable structure
Low temperature(< 55℃) reduces the stress on components
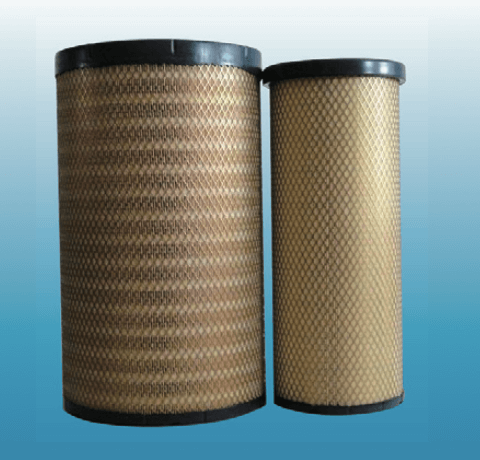
LOWER MAINTENANCE
Without Oil Air Separation Unit
Consumable parts are only air and water filter elements
$100~$300/year
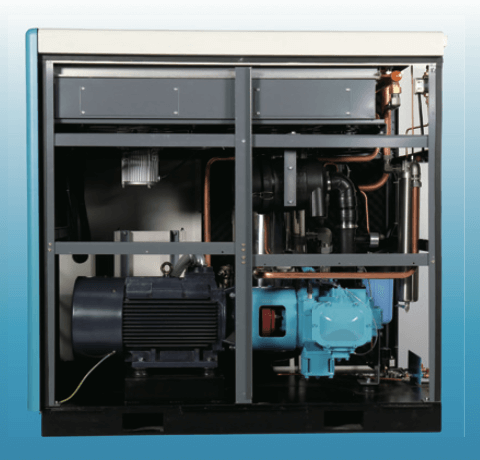
ENERGY SAVING>30%
Ideal isothermal compression and no heat waste(<55℃)
Most Advanced VSD and Two-stage compression technology
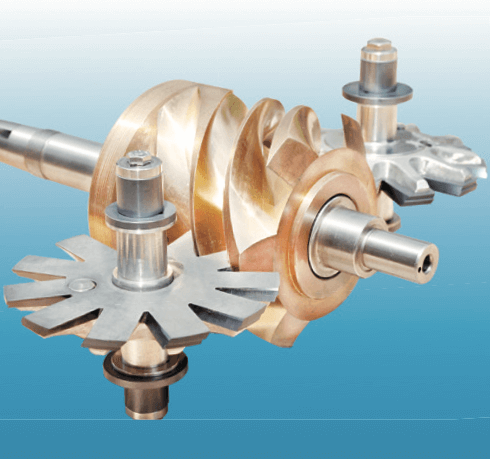
SUPER QUIET
Super dynamic balanced system
The motor and screw are directly connected
Sound absorbing materials are also used in the shell
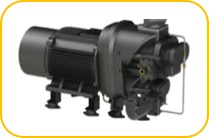
AIR END
Optimal profile
Double stage energy saving more than 10% than single stage.
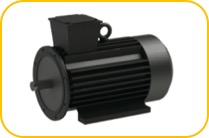
PM MOTOR
Direct Drive
Class 1 PM motor, Power factor: >95%, Oil-cooled type can be customized
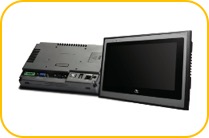
VSD CONTROL
Automatic operation
Dynamic display all operation parameters, prevent accidents by the alarm.
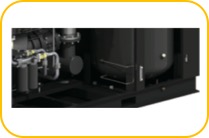
EASY-MAINTENANCE
Patent technologies
Filters can be easy replaced in half an hour. Oil can be completely replaced.
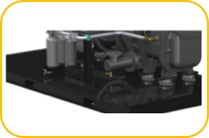
OIL SYSTEM
Minimum pressure drop
Patent oil storage device can guarantee the oil supply of the air end after a long shutdown.
How to choose the right air compressor?
Air Compressor Sizing
Whether you're starting your business or adding a new compressor to your setup, you need to choose the
Meeting Standards for Compressed air for Electrical Bus or Railway
You may not be aware of the fact that your everyday smooth railroad venture exclusively relies upon
What Is Ambient Pressure and Why Is It Important?
Many screw-type air compressors have an adjustable regulator screw. This screw controls the pressure of the compressed air
What to Look for in a Dental Air Compressor?
A dental compressor is a device that provides compressed air to any equipment requiring compressed gasses. It supplies
Air Compressor Horse Power
Most people assume that all air compressors are the same; however, this is not true. The horsepower of
Air-Cooled vs. Water-Cooled Compressor
In the procedure of compression of gases, the air compressor creates a lot of heat. The air compressors
We replaced 21 piston type compressors with one 40bar 10cubic Screw type compressor.
No more noise, no more spare parts and high maintenance fee.
We began to use their oil free type products since 1998, the products are very reliable.
Their Water-lubricated Screw Air Compressor can ensure the 100% oil free and clean compressed air for our processing, and ensure the high quality of our products.
The oil free type screw air compressor energy saving 38.6% compared with our used air compressor, and saving 25.8% compared with the new oil lubricated type screw air compressors.
“Class 0 oil-free air compressor guarantee the best quality of our end products”
“Electrical costs and maintenance fee is significantly reduced.”