Contents
Air compressors, like any other machine, demand routine maintenance. The advantage of servicing an air compressor is how simple it is. Your equipment will become more efficient for a more extended amount of time if you are doing repairs. You will also save time and restoration money in an emergency.
Compressed air energy is the ideal power source for intense workloads, considering its fundamental need for maintenance. Conventional air compressors use four to eight percent more power consumption to produce one horsepower of pressurized air. Furthermore, several elements cause air compressors to lose efficiency over time if they are not properly maintained.
How to Maintain the Efficiency of Air Compressor
How to Maintain the Efficiency of Air Compressor
-
Improve the Overall Design of Your System
Among the most essential things ineffectively ensuring an air compressor’s role is its design.
- The compressed air supply system’s structure and shape are crucial in guaranteeing optimum velocity and pressure supply to even the most remote juncture sites. Using corrosion-free, slick metal like Aluminum Pipes ensures optimal motion and pressure distribution. An extensive piping distribution network now can save cash and effort afterward if further development is envisaged.
- Reduce the path’s curves and angles from where air passes. Sharp twists raise the friction in the air compressor, which causes it to flare up and wear out components. This heat generation depletes the device’s vitality, resulting in more pressure decreases and, eventually, inefficient delivery. The equipment will expend little fuel and survive longer if the flow channel is straightened.
- With a heat exchanger, you can avoid wasting energy. Air compressors are only approximately 10% efficient; therefore, most of the energy is lost to heat. You may reuse virtually all of the expended electricity and utilize it to heat up your desk or other functions by installing a heat exchange unit.
- Leaks should be reduced or eliminated. Lack of compressed air because of breaches in the supply network not only leads to reduced strength at the need of use and the resulting effectiveness, but it also forces the compression system to operate better and longer to maintain an adequate level. An efficient leak control system may save your air system’s operating costs by much more than 25% to 30%.
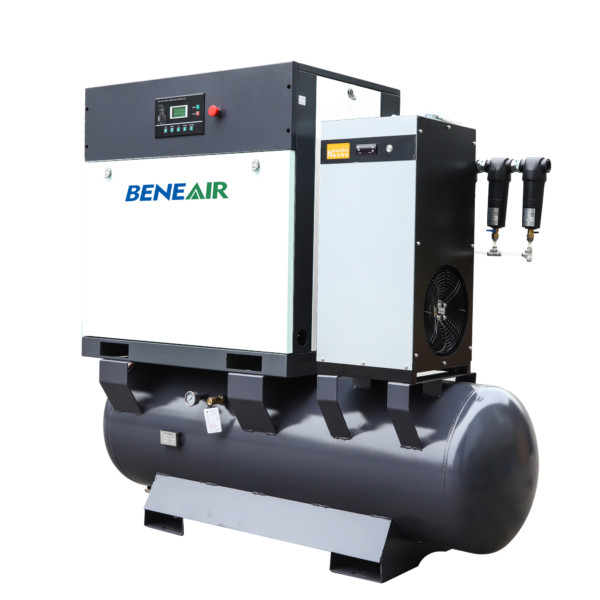
Make the Most out of Your Air Compressor’s Functions
Make the Most out of Your Air Compressor’s Functions
Compressors are designed to provide a specific airflow within a given pressure level, and the controls determine its potential to stop when they achieve that particular limit. An air compressor’s controls bridge the compressor’s production and the necessary workload. A perfectly alright monitoring system that can supply steady, usable air pressure near to the minimum requirement instead of the maximum is preferable.
- Based on the required volume, ON and OFF buttons command the compressor’s system to switch off as well as on.
- Load/unload settings function in collaboration with switch ON and OFF control systems to notify the compressor when it is time to release or stop pressure.
- Dual and automatic controllers allow you to choose between the switch ON and pause, as well as the load and unload controls.
- High-pressure air is stored in pressure/flow regulators, which may then be utilized to satisfy generating leads.
- Variable displacement permits the compressor to work in a variety of different loading situations.
- Master controls are used in devices with many units to synchronize all of the operations required to optimize compressed air.
- A compressor requires keeping track of its own necessities, like airflow, and modulating regulations enable the user to fine-tune this factor. On the other hand, multi-step controllers allow for operation without even a whole application of load.
- When the diversity of air compressors surpasses the capability of remote and regional controls, system master control systems might help. These controls can keep track of system components as well as statistics to help with repairs.
Maintenance of Air Compressor System
Maintenance of Air Compressor System
Servicing and maintenance are the most critical components in ensuring your air compressor’s efficient operation. Ensure that the compressor is in a safe, sterile environment. You should maintain cleaned filters and radiators and check the system regularly and implement the manufacturer’s instructions. Anything left undone with the air compressor will necessitate further repairs or maybe replacement sometime in the near future.
The air end, engine, driving system, oils, and filters are the main parts of the compressors that require regular maintenance.
- Air Ends
Pollutants in the airflow and grease, as well as extreme heat, wreak equipment air ends and their gears. Look for weird noises and movements. Sensors must be able to identify imminent issues and trigger warnings if necessary. Most companies advise upgrading air ends after some months to minimize pricey, unexpected breakdowns.
- Machine Bearings
Machine bearings must be greased with the appropriate amount and kind of lubricant at all times. Replacement of bearings should be done on a regular basis. Assess the current drain on a regular basis to make sure the engine is not overburdened. Appropriate aeration and external heat in the compressor chamber extend the motor’s life.
- Driving Systems
The alignment of the driving systems should be maintained. The imbalance of the structure or installation blocks will harm the connection. Equipment shafts must be greased at all times. Belts that are damaged or torn should permanently be changed.
- Lubrication
Lubes in any compressor chills encapsulate, shield, and eliminate impurities. To maintain optimal operational life, remove all previous oil before replacing. Oil should be changed according to the manufacturer’s recommendations for the situation. Oil samples regularly extend the life of the lubricants. Avoid using lubricants not developed for a particular engine since they can shorten its life.
- Filters and Filtration System
Filters and cleaners guard the machine against mechanical damage. The cost of efficient filtration is more petite than restoring broken equipment. Regularly maintain and change air intake filters. This practice enhances operational efficiency by reducing impurity and air end corrosion. The compressor’s capacity is reduced by about 1% when an input filtration system with a 1% increment of pressure change is used. Oil filters and extractors must be replaced and maintained regularly.
Leave A Comment