Contents
Do you remember that your mother cleaned the house thoroughly in the springtime? Spring cleaning is an annual cleaning of the house for many households. We thoroughly clean every part of the house and prepare it for the coming season.
Similarly, industrial systems also require a thorough cleaning which is never better than spring. General cleaning is important to save the compressed air system from damaging or poor performance, but don’t forget to do thorough maintenance of the system and prepare it for the rising temperatures.
What is a Screw Air Compressor?
What is a Screw Air Compressor?
Here is a checklist before you allow the compressed air system to run during the season. It’s a yearly maintenance plan that you must do in the spring.
Regulate the required voltage
Start with the voltage of the compressed air system. Check if it is getting the right voltage that is required by the system. Notice that the voltage must be optimal, neither higher nor lower than the required value.
If the voltage is higher than that required by the compressor, it will cause damage to the system and cost you more. On the other hand, if the voltage is too low than what is required for the machine to work properly, it will end up in an inefficient system that is not producing the desired results.
On average, an electric air compressor needs 110 to 120V, while a motor-run air compressor needs 220V. Regulate the voltage of your system according to its type and model.
Monitor temperature
Another important thing to check is the temperature of any electronic machine. The optimal temperature for a compressed air system should range between 50 to 85 degrees Fahrenheit.
Below this temperature, the system will lead to freezing, and above this temperature, it will end up overheating. In most cases, overheating is an issue. So check for overheating especially when preparing your machine for the summer season.
For this, you might inspect the cooling systems of the compressor. Two different types of compressed air systems use different cooling strategies; i.e., water cooling and air cooling. Moreover, heat exchangers in the system are an additional source to deal with this issue.
Check the reliability of these cooling systems and fix them so that your system does not overheat in summer. Also, check for any clogged pipes or vents which may be causing the temperature of the system to rise.
Navigate the compressor oil
After checking voltage and temperature, check if the oil of the compressed system is sufficient or not. Lubrication is an important part of machinery when it comes to its efficiency. Even when you have maintained each part of the air compressed system but ignored its lubrication, the system will be at risk of inefficiency.
It is important to assess that the oil needs to get replaced, otherwise it will cause the varnish to build up and overheat the system. When any part of the air-compressed system is poorly lubricated, it will struggle to perform effectively and end up overheating the system.
Varnish is the byproduct of oil degradation in the oil-based air compressed system. It usually happens when the oil is not changed for a long time and it starts degenerating.
Regardless of whichever high-quality lubricant you’re using, there are 99.9 chances of degradation. Poor lubrication, overheating, and varnish buildup is a vicious cycle that needs to be assessed timely to prevent more serious outcomes.
The oil change is a part of the yearly maintenance of the compressed system and there’s no time better than spring to nourish your system to work efficiently in summer. On average, you must do this after at least 1000 hours of usage.
Test the reliability of filters
Testing the filters is an important task in spring as the season comes and leaves with a lot of airborne particles that clog filters and cause problems in the flow of air. In this way, the working of the compressed air system compromises and ultimately increases costs.
Spring is the season that puts more stress on the filters to screen pollens and other tiny air particles. So changing the dirty and clogged filters in spring is a good idea to welcome the new season.
For changing the filters, unplug the machine and let it cool down. Then remove the top base and check the filter element thoroughly. Dust off the debris of the filter and make sure they are clean. If they are still not clean or you notice any clogged pores, replace the filters.
On average, filters should be changed after 2000 hours of usage. Don’t forget to check the oil filter as well if your compressor is oil-based.
Investigate if there are any leaks
Despite the fact that the compressor is the main part of an air compressed system, we can not overlook hose, pipes, and connectors. If the pipes are damaged or have holes in them, a rapid drop in pressure can occur without knowing the apparent cause of the misconduct.
A drop in PSI will increase the air demand and increase the overall cost. Not only this, but it will give a tough time to the compressor in producing efficient outcomes. Usually, air compressors come with a safety alarm if there is a severe drop in pressure. However, sometimes the leaks are too few to beep the safety alarm.
Still, you can not ignore these leaks as a small leak can cause drastic effects on your electricity bills. In such a case, you have to figure out the leakages yourself by following the look, listen and feel rule.
To detect the leaks, turn off the machine and stand closer to it. Carefully listen to any sound near the system and you’ll detect the leakage. Fix the leakage if any and tighten the connections to avoid energy wastage.
Drain the receiver tank
The receiver tank has served a lot the whole year. It would been full of water vapors until now. If you leave it as it is, the upcoming season loaded with humidity will be quite difficult for the compressor tank.
Clean the tank and drain out those vapors causing inefficiencies in the system. Open the drain valve by rotating the drain ring in a clockwise direction. Then clear out all the content present in the drain and let it air dry. After it is completely dry, seal the valve with the ring again.
Check if the safest option is working
The last thing you must check to quote the air-compressed system ‘ready for summer’ is checking its safety. Test if the auto-shutdown option is working. Also, make sure the performance of safety alarms.
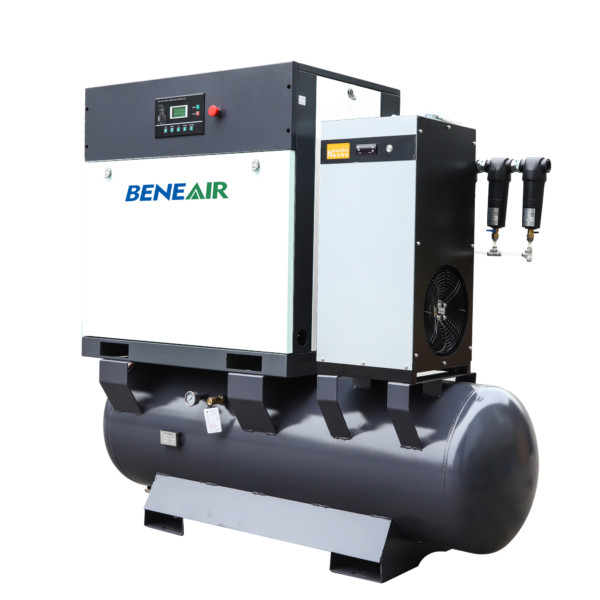
Leave A Comment