Air Compressor for Painting Industry
Paint sprayers are used in several industries such as construction industry, automotive industry, furniture industry, etc. The use of pneumatic air tools can make painting much effective, rapid, and easy. This can result in effective and efficient work. However, choosing the right air compressor can be challenging. There are many aspects including pressure and volume that need to be considered before using an air compressor for a particular job.
An air compressor is widely used for painting purposes now. There are many applications of air compressors in the paint industry, for instance, using an air compressor to paint cars, furniture, houses, for DIY hacks, and even painting crossovers on the roads.
Do you need
Class 0 Oil-free compressed air systems for your high-end painting industry?
Do you need
more convenient portable air compressor for your painting work?
We have more than 30 years’ experience.
How to Choose the Right Painting Air Compressor
Whilst choosing the right air compressor for painting, ensure that the air gun has the accurate pressure requirement and air consumption. These features of a spray gun depends on what these guns are being used for, for instance, furniture paint, car paint, etc. A spray gun used for automatic paint on cars will use relatively a lower consumption rate falling in the range of 7-15 CFM.
There are three types of air compressors that are used in the paint industry. These three include reciprocating, rotary screw, and centrifugal. Reciprocating Air Compressor is known as positive displacement machine – it can increase the pressure of the air by reducing its volume.
The second one is Rotary Screw Air Compressor which is also known as positive replacement compressor. It consists of two rotors in the casing and the rotors compress the air internally for effective working.
The third one is Centrifugal Air Compressor – it is a dynamic compressor based on the transfer of energy that is occupied by rotating the impeller to the air. It transfers energy and provides effective results.
Requirements of an Air Compressor for Spray Painting
An air compressor will ensure automatic painting and would ultimately be cost-effective, time-effective, and of course, would save a ton of manpower. Whilst choosing the right air compressor for your spray painting, you need to consider these three aspects as per your requirements.
PSI
While using an air compressor for spray painting, ensure that you have the right PSI. For this, you might need a low pressure ensuring that the delivered paint is even and unswerving. The ideal requirement of PSI in spray painting, rising to 40 PSI or more in some cases.
CFM
The most important factor to consider while presuming the requirements of an air compressor is the cubic feet per minute (CFM). It measures air volume produced by the compressor as per the minute. The spray coverage would be inconsistent and unstable if the CFM rating of the compressor is not higher than the CFM requirements on the spray gun. The ideal CFM requirement of an air compressor for spray painting is at least 12 CFM.
Tank Size
Lastly, the tank size plays a very important role in determining the proper functioning of the spray gun. It is highly considered since the spray gun requires a constant airflow rather than a recurrent one for proper painting. The ideal requirement of tank size in an air compressor to ensure even and stable spray painting is at least 50 gallons.
Portable VS Stationary Air Compressor
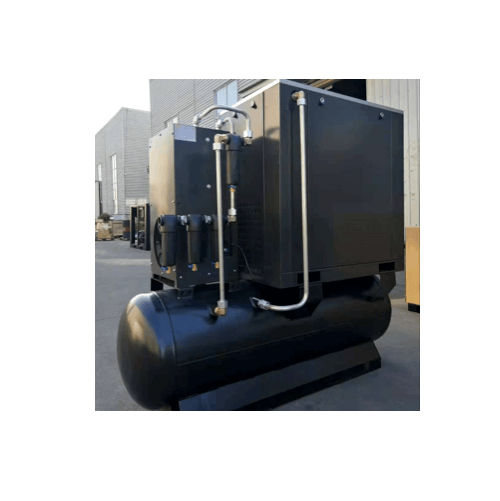
Brainstorm your requirements before buying an air compressor. You have a choice of either a portable one or a stationary one. If your work requires you to move a lot, for instance, house painting or other such services, we would recommend you a portable air compressor.
On the other hand, if you do all your painting in one location like an auto repair garage, a stationary air compressor will best suit your needs.
How to Spray Paint with an Air Compressor
Spray painting with an air compressor is very easy, handy, time-effective, and gives a better result than manual painting. Here is what you will need to start painting with an air compressor.
- Safety Gear: You need to ensure your safety. You would need a mask, goggles, and rubber gloves.
- An air compressor as per your requirements.
- Hose.
- Spray gun attachments.
Process of Using an Air Compressor
Step 1: Apply your safety gear before initiating the work to stay safe.
Step 2: Ensure proper connection of your air compressor with your spray gun via a hose and other attachments.
Step 3: Set an adequate CFM.
Step 4: Mix your paint to accurate ratios in order to use it.
Step 5: Do a quick test run by testing the pressure on a small cardboard piece. Adjust the pressure as per the requirement.
Step 6: Apply a subtle and even coat on your wall/ car/ furniture. Wait for it to dry and apply another even coat after 12/24 hours as the first coat has dried.
Advantages of an Air Compressor in Spray Painting
Here are a few advantages of air compressors in spray painting that you shouldn’t miss out:.
1. Time-Effective
Spray painting via air compressors can be extremely time saving. The pressure produced by the air compressor gives a smooth and thick layer of paint in one go. This results in painting of a bigger surface in a lesser time as compared to manual brush painting.
2. Spray Painting is forgiving
As the spray finish is made up of multiple thin layers, small scratches or blemishes are not as prominently visible as compared to a brush finish.
3. Offers Quality and Consistency
Spray painting with a fine air compressor can help you save time and get a consistent quality. Brush or roller marks are not a problem anymore. Spray painting mitigates the possibility of runs, drip, or air bubbles. A properly set up spray paint with an air compressor can help you get the perfect finish every time.
4. Provides Versatility
Spray painting is extremely versatile and can be applied to everything. Be it a car, furniture, a door, metal, or any other thing – spray paint can give you the perfect finishing. On the other hand, not all paints like automotive painting, etc. can be done by manual brushing.
5. Saves Manpower
In the case of manual brushing, you might need to apply 2-3 coats to get the perfect finishing. Although, spray paint would take only one coat to give you a thick and even coat. This would save the manpower to do a double or triple coat.
Common Equipment for the Textile Applications
- Air compressors have made work in the painting industry comparatively way easier, convenient, and rapid. In today’s era, you will not find any paint sprayer that doesn’t use air compressors. People are just really fond of the fact that air compressors have increased their convenience and decreased their hardships along with giving them a prominently better result than before.These air compressors can be used for both professional as well as personal use. There are many aspects it can be used in, including home maintenance, furniture painting industries, automotive industry, construction factories, and a lot more. All you need to do is ensure picking up the right attachments, and understanding the requirements of the air compressor you’re using for your task.
This is less time taking, less manpower usage, and rapid working – this is the reason that air compressors are replacing the manual work in the paint industry.
- If the compressed air will be applied to high-end painting industry, we suggest using 100% Oil-free type air compressor with the air dryer and filters.
- For the painting work without high requirements, if with a limited budget, the oil-lubricated type air compressor with refrigeration air dryer and filters can be chosen, but for long term consideration, an oil-free type air compressor can not only produce high-quality oil-free and clean air but also costs lower for maintenance and energy.
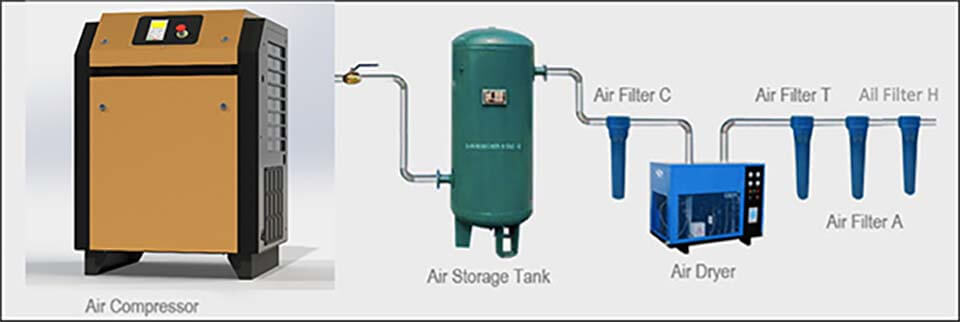
Related Products
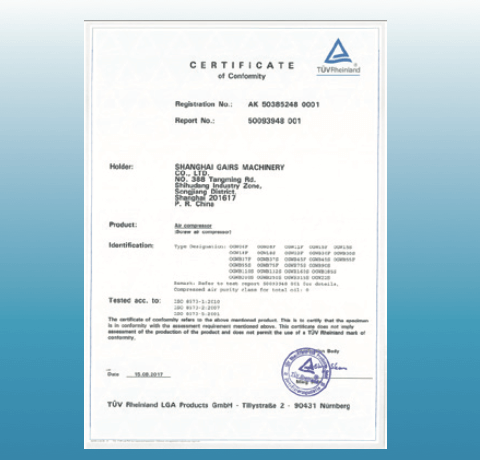
100% OIL-FREE
More than 20 years experiences in Water-lubricated Oil-free technology
Germany Rhineland TUV Class 0 Oil-free Certification
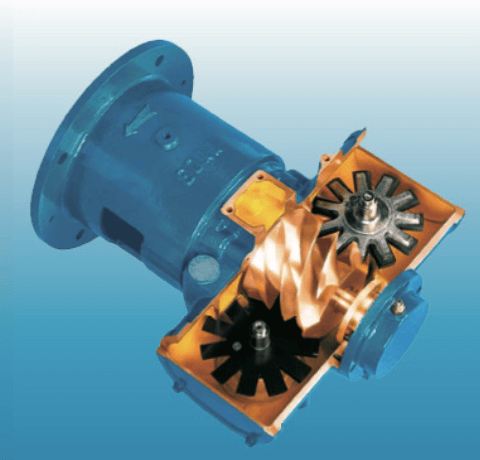
RELIABLE
More than 30 years Single Screw Technology
Most balance and reliable structure
Low temperature(< 55℃) reduces the stress on components
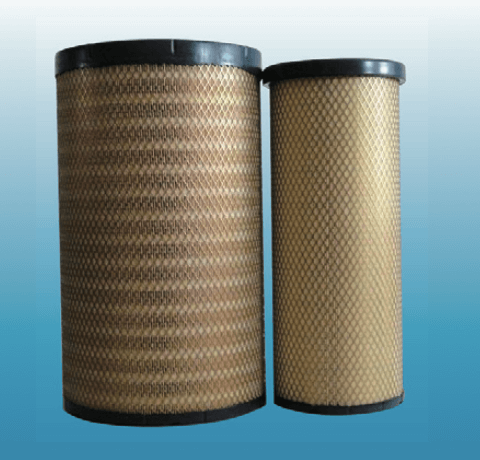
LOWER MAINTENANCE
Without Oil Air Separation Unit
Consumable parts are only air and water filter elements
$100~$300/year
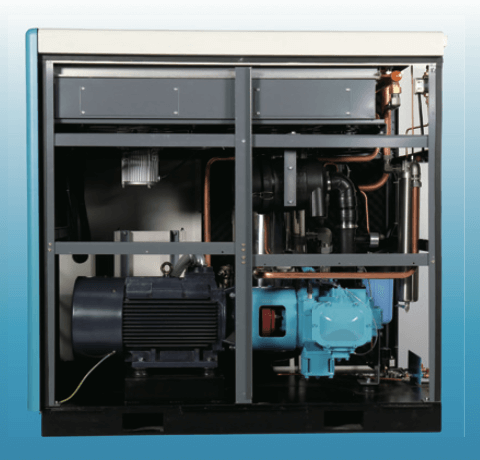
ENERGY SAVING>30%
Ideal isothermal compression and no heat waste(<55℃)
Most Advanced VSD and Two-stage compression technology
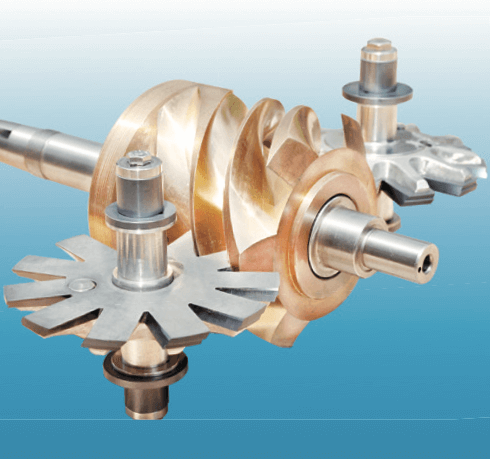
SUPER QUIET
Super dynamic balanced system
The motor and screw are directly connected
Sound absorbing materials are also used in the shell
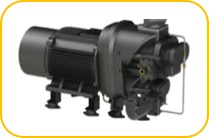
AIR END
Optimal profile
Double stage energy saving more than 10% than single stage.
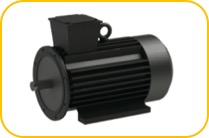
PM MOTOR
Direct Drive
Class 1 PM motor, Power factor: >95%, Oil-cooled type can be customized
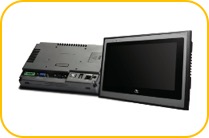
VSD CONTROL
Automatic operation
Dynamic display all operation parameters, prevent accidents by the alarm.
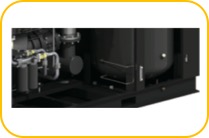
EASY-MAINTENANCE
Patent technologies
Filters can be easy replaced in half an hour. Oil can be completely replaced.
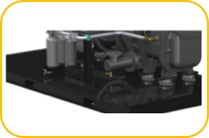
OIL SYSTEM
Minimum pressure drop
Patent oil storage device can guarantee the oil supply of the air end after a long shutdown.
How to choose the right air compressor?
Air Compressor Buyer’s Guide
As a common source of power, air compressors are widely used in various industries. Most manufacturing facilities need
How to Choose Water-cooled vs. Air-cooled for air Compressors?
The air compressor generates a lot of heat in the process of compressing the gas, there are several
Variable-speed VS. Fixed-speed Air Compressor
More and more people choose or update a VSD (Variable speed drive) or VFD (Variable frequency drive) air
Oil-free VS Oil-injected Screw Air Compressor
What is the difference between an oil-free and oil-lubricated air compressor? The difference is the oil
Water-injected Oil-free VS Dry Oil-free Screw Air Compressor
In recent decades, there has been more and more research on the oil-free screw air compressor. According to
Single-screw VS Twin-screw Air Compressor
When it comes to the screw type air compressor, generally, there are two kinds, single-screw type
We replaced 21 piston type compressors with one 40bar 10cubic Screw type compressor.
No more noise, no more spare parts and high maintenance fee.
We began to use their oil free type products since 1998, the products are very reliable.
Their Water-lubricated Screw Air Compressor can ensure the 100% oil free and clean compressed air for our processing, and ensure the high quality of our products.
The oil free type screw air compressor energy saving 38.6% compared with our used air compressor, and saving 25.8% compared with the new oil lubricated type screw air compressors.
“Class 0 oil-free air compressor guarantee the best quality of our end products”
“Electrical costs and maintenance fee is significantly reduced.”